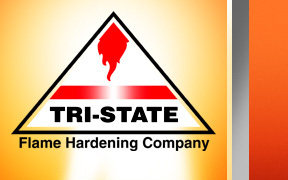










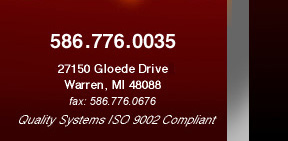
|
Flame
Hardening
Steel Alloys and Rolls! Cast and Ductile Irons!
A
surface hardening process in which heat is applied by a high temperature
flame followed by an appropriate quenching medium.

Tri-State's heat treating
process on alloy steels, cast and ductile irons results in a hardening
of the treated surface up to 1/8 inch deep, with minimal distortion. There
are a host of benefits: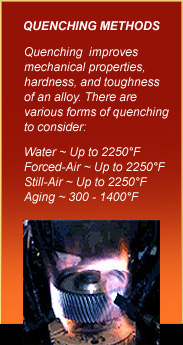
Increased
wear ability
Reduced downtime
and maintenance
Increased
production efficiency
Less distortion
Reduced finishing
operations
Shorter processing
times
The Flame Hardening Process has four basic types:
Stationary Flame Hardening
Stationary flame hardening requires that the specified area be heated.
Then the part is taken to quench or quench is brought to the part. This
method is particularly well-suited for shaft ends, special steel casting
configurations and large parts.
Progressive Flame Hardening
Progressive flame hardening involves the use of a flame head with integrated
quench capability. The heat/quench head is moved along the part by various
methods. This method is particularly well-suited for ways, flats, knives,
and rolls.
Spin Hardening
Spin flame hardening requires the specified area being treated to be spun
in front of the flame source. Then the part is then taken to quench. This
method is particularly well-suited for gears, wheels and sprockets.
Combination Hardening
Combination flame hardening couples the progressive and spinning methods.
The part being treated spins in front of the flame/quench head(s) and
at the same time the flame/quench head(s) move along the length of the
part.
Call Tri-State Flame
Hardening Company for your hardening applications today! We're easy to find in Macomb County, Michigan. Click HERE to find us.
|
|